在一次起重機轉臺試驗中,使用中短臂、基本臂兩個臂段的最大力矩工況吊載,按《GB/T 3811-2008》規(guī)范施加 5% 側載力,在吊載回轉過程中,起重機轉臺處發(fā)出“嘣、嘣、嘣”異響聲。異響聲能被人清楚的辨別,易引起客戶的抱怨,為此需要對此問題進一步分析。
1 分析問題階段
1.1 測量聲音來源
使用聲源定位設備,采用同樣的起重工況再進行測量,測量現場及結果如圖 1、2 所示,聲源位于轉臺底板與側立板交接位置。由于轉臺體在此處是一個箱形結構,箱形內部有加強板組合成的焊接結構,需要對此位置進一步分析。
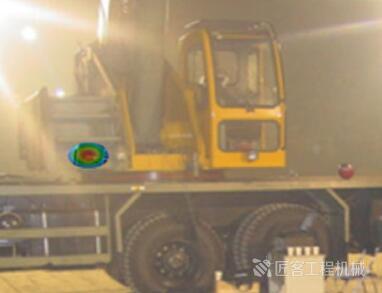
圖 1 轉臺底板處異響
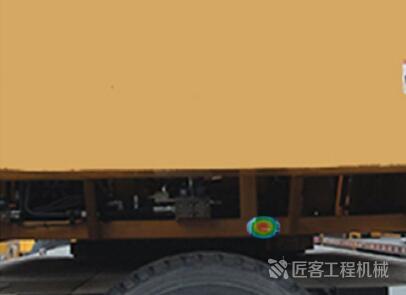
圖 2 底板異響側面位置
1.2 有限元在轉臺分析中的應用
使用的轉臺為框架式結構,它采用不同的鋼板組合拼焊而成。由于已初步確定異響源的位置,只需重點分析轉臺底板的箱形結構位置處的應力。轉臺結構如圖 3 所示。
根據《起重機設計規(guī)范》可知,產生異響轉臺使用的高強度焊接結構鋼許用應力 [σ] 推薦值為 460MPa。
對于轉臺結構體進行應力分析,采取離散逼近的方式,將其離散為有限個標準幾何單元的組合,分析單元的內力與外力,建立基于節(jié)點的單元受力平衡方程并求解。轉臺結構很復雜,劃分后節(jié)點數量非常多,而且需確保計算的收斂性、高效性和結果誤差度,為此使用有限元分析軟件完成計算過程。
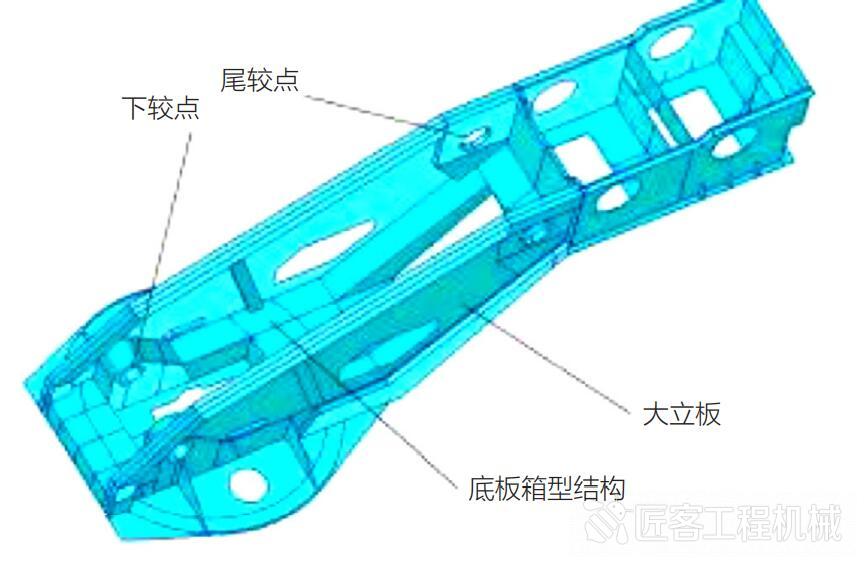
圖 3 轉臺結構
2 結果分析及優(yōu)化
2.1 轉臺受力分析
對轉臺結構體進行有限元分析,得到有限元分析結果,其用應力云圖顯示如圖 4、圖 5 所示。
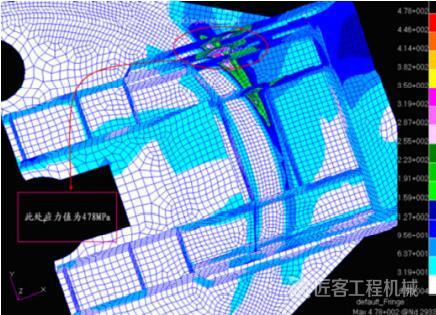
圖 4 底板應力云圖
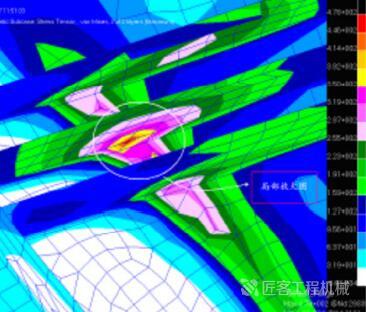
圖 5 側板應力云圖
2.2 轉臺應力結果
根據測量的聲音源位置,結合有限元分析的應力云圖,可知聲音在圖 4、圖 5 橢圓圈所示位置傳出。此處應力峰值達到 478MPa,而材料 HG785D 的許用應力 [σ] 推薦僅為 460MPa,峰值已超出許用應力范圍。這表明雖然材料的整體還處于彈性范圍,但此處已有微裂紋等缺陷產生,同時發(fā)出聲發(fā)射信號,也就是所聽到的轉臺異響聲。
2.3 轉臺聲源處應力下降方案
在原轉臺基礎上,制定了 3 個改進方案,以降低應力強度因子幅度。方案一如圖 6 所示,即改變斜置加強板的位置,由支承在底板加強板內側位置改為外側位置,從而加大此處的截面模量。方案二如圖 7 所示,即在方案一的基礎上,去掉在轉臺立板內側一塊加強板,同時減小焊接應力集中。方案三如圖 8 所示,即改變應力集中位置的立板結構,改用一個小箱形結構替代它。
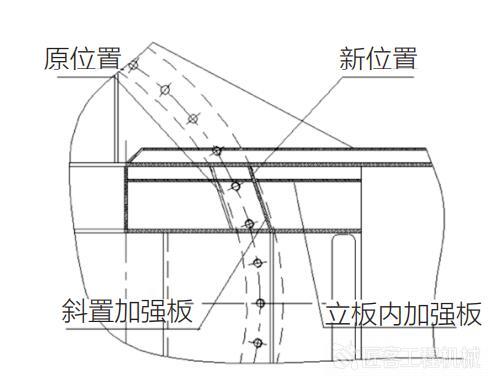
圖 6 改進方案一
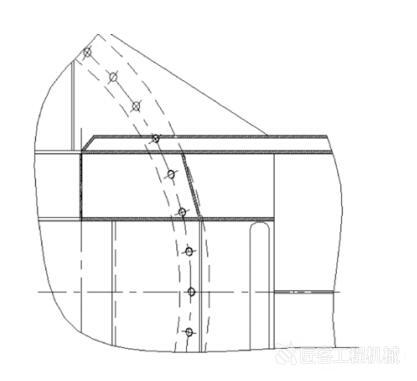
圖 7 改進方案二
2.4 轉臺不同方案應力值結果及分析
對以上 3 種方案分別進行分析。其有限元分析結果分別如圖 9、圖 10、圖 11 所示。
圖 9 所示的方案一中,最大應力值仍然在箱形結構中應力集中位置,峰值由 478MPa 下降為 305MPa,下降幅度為 36%,表明該方案有效。轉臺底板回轉支承加強座圈板為環(huán)形結構,斜置加強板在內側時,來自于轉臺尾鉸點受力往下傳遞至轉臺底板位置時,存在附加力矩的作用。當加強板移至環(huán)形外側時,附加力矩得到有效減小。在圖 10 所示的方案二中,應力集中位置的應力峰值由 478MPa 下降為 263MPa,下降幅度為 45%。這驗證了斜置加強板在底板加強環(huán)形板的位置,為主要影響因素。方案二相比方案一,去掉了轉臺立板內側的一塊加強板,應力由 305MPa 下降為 263MPa,下降幅度為 13.8%。這說明沿應力最大位置分布在近似垂直的位置,立板間距布置狀況也起著一定的作用。方案二去掉了一塊立板后,最大應力區(qū)域范圍明顯擴大,受力更均勻,故減小了最大應力峰值??紤]在實際制造過程中,立板之間距離較小時,焊接較為困難。在交錯焊縫較多時,附加焊接應力較高,更易導致原轉臺中應力峰值增大,從而引起異響。在圖 11 所示的方案三中,應力峰值由 478MPa 下降為393MPa,下降幅度為 17.8%。此方案中,箱形結構的截面模量得到優(yōu)化,但僅靠增加立板的板厚,對應力峰值的改善效果并不理想。立板間距的改變,只適當改變了底板位置的應力分布,難以達到大幅降低應力峰值的作用。
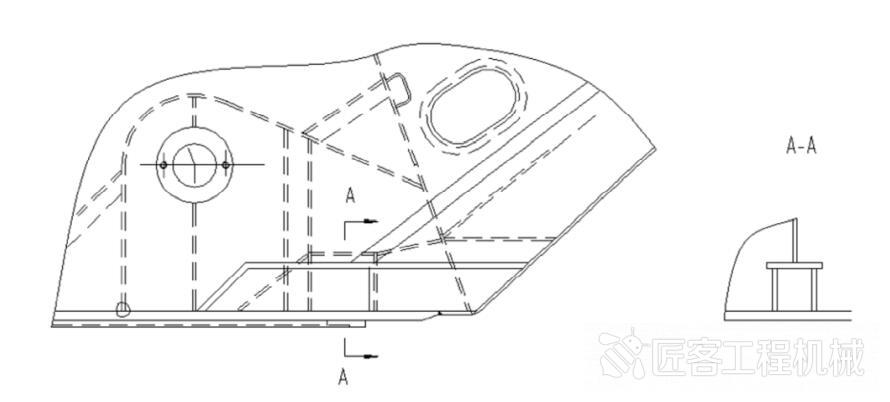
圖 8 改進方案三
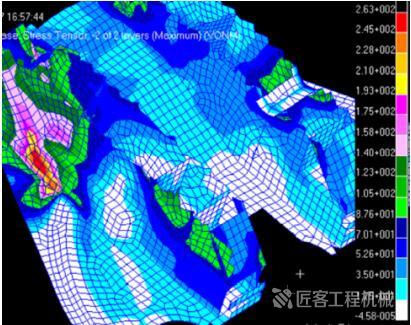
圖 9 方案一有限元分析
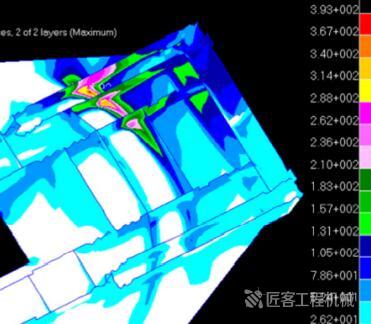
圖 10 方案二有限元分析
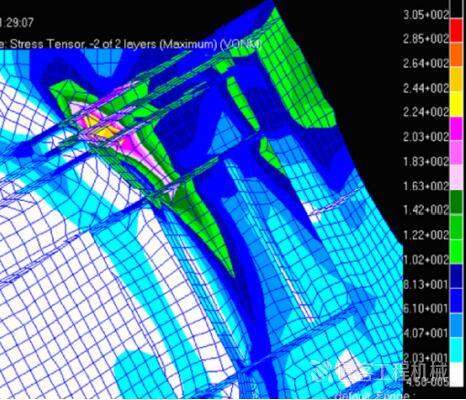
圖 11 方案三有限元分析
2.5 轉臺方案實際應用
根據以上分析可知,斜置加強板位置是應力強度的主要影響因素,立板及立板加強板位置及間隔是次要影響因素。斜置加強板在底板梯度變化處沿圓周布置效果最佳。
分別按上述方案制造轉臺,并進行驗證。方案一、二在相同試驗工況反復吊載,異響聲未再出現。這表明當應力值低于 305MPa 時,能夠產生聲發(fā)射的能量值較小,微裂紋的擴展速率較低,不足以產生人耳可感受的聲發(fā)射。按方案三試驗時,異響聲再次出現,但異響聲強度比原轉臺弱。這表明應力值為 393MPa 時,重載荷情況下不可避免產生微裂紋,但裂紋的擴展速率有所降低,聽到的異響
聲也相應減小。根據方案一中應力值 305MPa(為材料推薦值 [σ] 的 2/3)計算,考慮在一定的安全系數范圍內,推薦轉臺底板應力敏感集中區(qū)域應力設計值應小于 0.7[σ] 。
實際應用的轉臺以方案二為基礎,適當增加立板加強板的厚度并進行優(yōu)化后,再進行可靠性試驗,轉臺底板位置未出現明顯的異響聲,檢查未出現開裂,由此驗證最終方案可行。
來源《工程機械與維修》2019年第六期
修機|起重機轉臺重載時底板處異響的消除
匠客工程機械 評論(0)
來源:匠客工程機械
在一次起重機轉臺試驗中,使用中短臂、基本臂兩個臂段的最大力矩工況吊載,按《GB/T 3811-2008》規(guī)范施加 5% 側載力,在吊載回轉過程中,起重機轉臺處發(fā)出“嘣、嘣、嘣”異響聲。異響聲能被人清楚的辨別,易引起客戶的抱怨,為此需要對此問題進一步分析。
1 分析問題階段
1.1 測量聲音來源
使用聲源定位設備,采用同樣的起重工況再進行測量,測量現場及結果如圖 1、2 所示,聲源位于轉臺底板與側立板交接位置。由于轉臺體在此處是一個箱形結構,箱形內部有加強板組合成的焊接結構,需要對此位置進一步分析。
圖 1 轉臺底板處異響
圖 2 底板異響側面位置
1.2 有限元在轉臺分析中的應用
使用的轉臺為框架式結構,它采用不同的鋼板組合拼焊而成。由于已初步確定異響源的位置,只需重點分析轉臺底板的箱形結構位置處的應力。轉臺結構如圖 3 所示。
根據《起重機設計規(guī)范》可知,產生異響轉臺使用的高強度焊接結構鋼許用應力 [σ] 推薦值為 460MPa。
對于轉臺結構體進行應力分析,采取離散逼近的方式,將其離散為有限個標準幾何單元的組合,分析單元的內力與外力,建立基于節(jié)點的單元受力平衡方程并求解。轉臺結構很復雜,劃分后節(jié)點數量非常多,而且需確保計算的收斂性、高效性和結果誤差度,為此使用有限元分析軟件完成計算過程。
圖 3 轉臺結構
2 結果分析及優(yōu)化
2.1 轉臺受力分析
對轉臺結構體進行有限元分析,得到有限元分析結果,其用應力云圖顯示如圖 4、圖 5 所示。
圖 4 底板應力云圖
圖 5 側板應力云圖
2.2 轉臺應力結果
根據測量的聲音源位置,結合有限元分析的應力云圖,可知聲音在圖 4、圖 5 橢圓圈所示位置傳出。此處應力峰值達到 478MPa,而材料 HG785D 的許用應力 [σ] 推薦僅為 460MPa,峰值已超出許用應力范圍。這表明雖然材料的整體還處于彈性范圍,但此處已有微裂紋等缺陷產生,同時發(fā)出聲發(fā)射信號,也就是所聽到的轉臺異響聲。
2.3 轉臺聲源處應力下降方案
在原轉臺基礎上,制定了 3 個改進方案,以降低應力強度因子幅度。方案一如圖 6 所示,即改變斜置加強板的位置,由支承在底板加強板內側位置改為外側位置,從而加大此處的截面模量。方案二如圖 7 所示,即在方案一的基礎上,去掉在轉臺立板內側一塊加強板,同時減小焊接應力集中。方案三如圖 8 所示,即改變應力集中位置的立板結構,改用一個小箱形結構替代它。
圖 6 改進方案一
圖 7 改進方案二
2.4 轉臺不同方案應力值結果及分析
對以上 3 種方案分別進行分析。其有限元分析結果分別如圖 9、圖 10、圖 11 所示。
圖 9 所示的方案一中,最大應力值仍然在箱形結構中應力集中位置,峰值由 478MPa 下降為 305MPa,下降幅度為 36%,表明該方案有效。轉臺底板回轉支承加強座圈板為環(huán)形結構,斜置加強板在內側時,來自于轉臺尾鉸點受力往下傳遞至轉臺底板位置時,存在附加力矩的作用。當加強板移至環(huán)形外側時,附加力矩得到有效減小。在圖 10 所示的方案二中,應力集中位置的應力峰值由 478MPa 下降為 263MPa,下降幅度為 45%。這驗證了斜置加強板在底板加強環(huán)形板的位置,為主要影響因素。方案二相比方案一,去掉了轉臺立板內側的一塊加強板,應力由 305MPa 下降為 263MPa,下降幅度為 13.8%。這說明沿應力最大位置分布在近似垂直的位置,立板間距布置狀況也起著一定的作用。方案二去掉了一塊立板后,最大應力區(qū)域范圍明顯擴大,受力更均勻,故減小了最大應力峰值??紤]在實際制造過程中,立板之間距離較小時,焊接較為困難。在交錯焊縫較多時,附加焊接應力較高,更易導致原轉臺中應力峰值增大,從而引起異響。在圖 11 所示的方案三中,應力峰值由 478MPa 下降為393MPa,下降幅度為 17.8%。此方案中,箱形結構的截面模量得到優(yōu)化,但僅靠增加立板的板厚,對應力峰值的改善效果并不理想。立板間距的改變,只適當改變了底板位置的應力分布,難以達到大幅降低應力峰值的作用。
圖 8 改進方案三
圖 9 方案一有限元分析
圖 10 方案二有限元分析
圖 11 方案三有限元分析
2.5 轉臺方案實際應用
根據以上分析可知,斜置加強板位置是應力強度的主要影響因素,立板及立板加強板位置及間隔是次要影響因素。斜置加強板在底板梯度變化處沿圓周布置效果最佳。
分別按上述方案制造轉臺,并進行驗證。方案一、二在相同試驗工況反復吊載,異響聲未再出現。這表明當應力值低于 305MPa 時,能夠產生聲發(fā)射的能量值較小,微裂紋的擴展速率較低,不足以產生人耳可感受的聲發(fā)射。按方案三試驗時,異響聲再次出現,但異響聲強度比原轉臺弱。這表明應力值為 393MPa 時,重載荷情況下不可避免產生微裂紋,但裂紋的擴展速率有所降低,聽到的異響
聲也相應減小。根據方案一中應力值 305MPa(為材料推薦值 [σ] 的 2/3)計算,考慮在一定的安全系數范圍內,推薦轉臺底板應力敏感集中區(qū)域應力設計值應小于 0.7[σ] 。
實際應用的轉臺以方案二為基礎,適當增加立板加強板的厚度并進行優(yōu)化后,再進行可靠性試驗,轉臺底板位置未出現明顯的異響聲,檢查未出現開裂,由此驗證最終方案可行。
來源《工程機械與維修》2019年第六期
敬請關注 《工程機械與維修》&《今日工程機械》 官方微信
更多精彩內容,請關注《工程機械與維修》與《今日工程機械》官方微信